Click to Download PDF Copy (ENGLISH)
QUALITY MANAGEMENT SYSTEM
This document is confidential. The copyright therein is vested in Location x rent a car
Recipients must obtain the written authority of the said company before wholly or partly duplicating these contents or disclosing the same to others.
REVISION LOG
REVISION |
PAGES REVISED |
COMMENTS |
|
|
|
|
|
|
|
|
|
|
|
|
TABLE OF CONTENTS |
PAGE |
1. QUALITY POLICY STATEMENT |
|
2. INTRODUCTION |
|
3. SCOPE |
|
4. PURPOSE |
|
5. ABBREVIATION |
|
6. DEFINITIONS |
|
7. REFERENCE |
|
8. PROJECT ORGANISATION AND RESPONSIBILITIES |
|
9. QUALITY PLAN |
|
10. PROCUREMENT |
|
11. MATERIAL CONTROL |
|
12. MATERIALS IDENTIFICATION,TRACEABILITY AND PRESERVATION |
|
13. INSPECTION AND TESTING |
|
14. LEVEL OF INSPECTION |
|
15. CONTROL OF MONITORING MEASURING DEVICES |
|
16. CONTROL OF NON-CONFORMANCE |
|
17. PREVENTIVE AND CORRECTIVE ACTIONS |
|
18. INTERNAL QUALITY AUDITS |
|
19. DOCUMENT CONTROL |
|
20. QUALITY RECORDS MANAGEMENT |
|
21. MANAGING REVIEW |
|
22. PROJECT MEETINGS |
|
|
|
|
|
INTRODUCTION
The purpose of this Quality Policy is to establish the reference framework that allows the development of tools focused on achieving the highest levels of satisfaction for Location X Rent a Car clients and partners, through the continuous improvement of the services provided and the means used.
For this reason, Location X Rent a Car Management has committed to implement, maintain, and continuously improve a Management System based on the requirements of the ISO 9001 standard
Quality of Service is one of the fundamental values of Location X Rent a Car, with ensuring the best customer experience being one of its main objectives.
Main commitments.
Through this Quality Policy, the management of Location X Rent a Car undertakes to: Analyse the organizational environment to understand client needs in order to adapt to them and ensure their satisfaction.
- Continuously analyse requirements in terms of the application of new technologies and work methods that have an impact on greater efficiency of our processes, and our improvement.
- Review and analyse compliance with the objectives and goals of the management system and, where appropriate, establish new objectives that are consistent with this policy.
- Identify and assess the risks arising from the provision of services.
- Carry out periodic reviews of both the System and the Policy in order to ensure their correct adaptation.
- Comply with the legal and regulatory requirements that affect the services offered.
- Implement a work methodology based on prevention and not correction, aimed at achieving constant improvement and evolution in professional development and services.
- Ensure that employees have sufficient training and motivation, in order to improve the processes, the workforce itself, and the objectives set.
- Form a compact a , professional, team that is perfectly integrated into the company’s philosophy.
- Address the claims and suggestions of our clients and partners, which will result in improvements with perceivable impact for the end customer.
- Make the Quality Management System an unwaivable pillar of our conduct.
ABBREVIATIONS:
Non Conformance Report |
NCR |
Health Safety and Environment |
HSE |
Quality Assurance and Quality Control |
QA/QC |
LOCATION X RENT A CAR |
LXR |
DEFINITIONS
COMPANY |
The owner of the CONTRACT in any instance |
CONTRACTOR |
The Company to which the CONTRACT WORK has been awarded and in this instance LOCATION X RENT A CAR |
CONTRACT |
The package of Contract Agreement signed between contract insurer and the CONTRACTOR (LOCATION X RENT A CAR) |
PROJECT |
Refers to all works and activities pertaining to the CONTRACT WORK |
QUALITY |
Is the degree to which a set of inherent characteristics fulfill requirements stated and implied needs are the inputs to developing project requirements. |
GRADE |
Grade is a category assigned to products or services having the same functional use but different technical characteristics e.g. grade of concrete. |
REFERENCES
ISO 9001:2015 – Quality management system
BS 5882- Total Quality Assurance Programme (1 day training for all the staff in Quality Assurance and Quality Control – mostly likely given by our third party angency in relation to bought items.
QMS PROJECT ORGANIZATION AND RESPONSIBILITIES WITH QMS WORKFLOW CHART
LOCATION X RENT A CAR organization structure is as shown below. It comprises of the Managing Director, Project Manager, Site Engineer, QA/QC Rep, HSE Coordinator, foremen, and field workers, all work as a team to deliver the project as expected by the client.
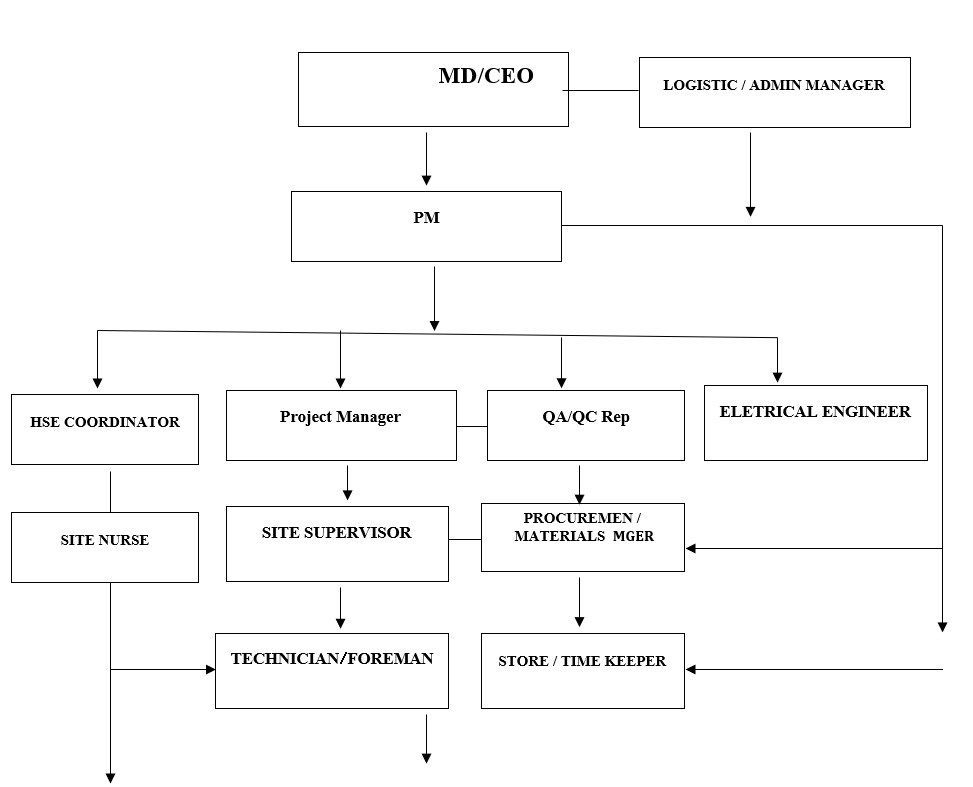
RESPONSIBILITIES
A Managing Director
- To plan and to organize the general technical requirements of the project.
- To assign project resources as required by the project.
- To prepare and review the contract documents.
- To prepare schedules, estimates and forecasts.
B Project Manager
- He is the day-to-day interlocutor of the project.
- He organizes and supervises the Technical, Plant, the Driving, the Administrative departments and has authority on QA/QC, HSE and Finance department for day to day works/coordination.
- He ensures that works are done under sufficient supervision by qualified workers using specified methods, materials and equipment and applying quality, safety and environment rules.
- He is to advise management of status changes that substantially affects any aspect of the project.
- He reports to the managing Director.
C Project Manager
- Coordination of all Project activities at site
- He is to give guidance to the organization and encourage total quality awareness.
- He shall mandate all staff of the company to adhere and implement the requirement of this manual.
- Has full authority to implement and direct quality system procedure.
- Account for the frequency, severity and cost of errors, non-compliance and deficiencies incurred by the project.
- Delegate duties to respective project personnel to expedite effective quality assurance programs.
- Execute corrective actions to improve quality deficiencies as designed by the QA/QC Officer.
- Reports to project manager
D Quality Assurance/Control Officer
- He is responsible for the total quality awareness in the company
- He establishes quality objective and policies
- He is reporting to the Project Manager and the Managing Director
- He is responsible for the total quality awareness in the company
- He establishes quality objective and policies
- He develops, and introduces improved quality system, manuals, and Procedures.
- He plans and conducts quality control and assurance audit system
- He analyses non-conformance of quality procedure, quality problems, clients problems, and determine structural improvement.
- Encourage management review of the company quality systems.
- Deals with internal/external audits, certification, publication, etc.
- Improves internal familiarity with quality system, quality awareness and training.
- Ensure adequate documentation, and archiving of records for the company.
- Disseminate information relating to quality to all staff
- Have full custody of all documents and documents control.
- Inform and advice the management on the deficiencies and errors arising from the project and measures to be taken to correct them.
- Perform assigned task in an orderly manner, obey all instruction and avoid taking risks that could jeopardize the job quality standard.
- Assign Quality control personnel to various areas of activity to monitor quality and progress of work.
- He shall ensure that within the scope of the contract, quality control inspection and approvals on materials, equipment and Driving activities are done.
E. Site Supervisor
- Responsible to the Project Manager
- Examine and make sure that selection of materials, personnel and equipment will ensure minimal errors in the execution of the project
- Take part in regular internal consultation relating to quality system procedures as regards the project at hand.
- Ensure proper handling, reporting, documentation, and presentation of evidences and necessary claims on deficiencies on the project.
- Ensure proper disciplinary action up to and including dismissal of any staff failing to comply with company quality assurance and control procedures.
- He shall be charged with the duties of monitoring quality inspection and work progress.
- He shall be charged with the duties of reporting actual progress, documenting it, and verify upon completion of work that all requirements have been met and that the required Quality records have been collated and filed.
- Quality Control inspections on materials, and equipment.
- He shall be responsible for inspection, reporting and initiation of non- conformance reports, Corrective Action Reports and Preventive Reports when required.
F. Procurement Officer
- The Material Controller has the following duties and responsibilities in the project:
- To coordinate all procurement activities inside the project, namely purchasing expediting, inspection and traffic / haulage.
- To coordinate and ensure correct and timely interfaces between the project procurement section and the project.
- To report to Project Manager all procurement activities.
- To manage procurement project personnel resources and work load.
- To define the project procurement plan taking into account sourcing of equipment, materials and services, and quality policy requirements.
- To ensure that timely expediting and inspection are taken.
- To initiate / sign all documents, reports and status drafted by project procurement personnel.
G. HSE Coordinator
- The HSE coordinator is responsible for all Health, Safety and Environmental issues and reports to the Project Manager. He is responsible for:
- Implementation of HSE policy.
- Projects Health, Safety and Environment plan.
- Management and workplace procedures (sites).
- Risk Assessment and Implementation of Recommended procedures.
- Planning, Execution, Control and Correction.
- Ensuring that Permit to work is made available where necessary.
- Safety Talks and Safety Walkabout.
- Training, personnel qualification, induction and training courses.
- Communication of HSE policies and other matters.
QUALITY PLAN
This plan describes outlines to be included in the project scheduled to ensure that the required quality criteria are consistently adhered to; the plan identifies the objectives, criteria, regulations and standards that need to be satisfied. It also states the parameters to be achieved. This plan also defines the measures that will be put in place to ensure that quality objectives are attained. These measures include but are not limited to procedures, organization, resources, skill and equipment.
PROCUREMENT
Procurement documents shall clearly state technical, commercial and Quality Assurance requirements, the Quality Assurance requirement shall of course be commensurate with the specified quality level rating of other items being procured. The technical requirement shall state instruction for the designing, manufacturing, installing, inspecting, cleaning, packaging, handling, shipping and storage as necessary they shall also state the design parameters of the item, design codes and industrial standards, the documents, certificates and the records to be prepared, kept and submitted for review approved by LOCATION X RENT A CAR
All relevant certificates, inspection Reports etc. that are generated from the inspections and tests shall be considered as QA/QC Records. No material or equipment shall be accepted on the Driving site and transferred to the store area unless it can be identified to a particular document that proves that the item has been inspected and had passed inspection. Inspection checklist shall be issued to show inspection requirements during Driving and installation.
MATERIAL CONTROL
All materials delivered to the site shall undergo proper identifiation and verification practice as to ensure conformity to Project Specifications. Appropriate preservation procedures shall be applied to ensure that the identity and the quality of stored material are maintained at all times. When detected, non-conforming material shall be identified by clears physical marking and if possible, segregates to prevent unauthorized or mixing with conforming material.
Purchased items shall comply with the requirements of the procurement document and verification shall be by inspection and other specified method. The result of verification shall be documented. The quality records, certification and documented verification for compliance with the requirements of the procurement documents.
MATERIALS IDENTIFICATION, TRACEABILITY AND PRESERVATION PROCEDURE
LOCATION X RENT A CAR shall ensure that materials are identified or segregated and stored to preserve the original condition and markings without deterioration, identification markings may include the use of stickers / colour tape appropriate to the type of product and area of manufacture / installation.
Material controller shall receive materials arriving at the job site and signs all delivery documents. All delivery documents covering packaged shipment received in apparently good order shall be stamped “Received Subject to Inspection for Concealed Damage”. If packaged shipments received are damaged, this shall be documented in the receiving inspection report.Materials received shall be positively identified against the purchase order.
Assigned Material Controller shall inspect the received materials according to their field of responsibility. Material Receiving Inspection Report shall be prepared after the completion of inspections. The copy of materials receiving inspection report will be issued to COMPANY for review and Joint Inspection if request shall be arranged.
Material Controller shall ensure that the materials received are tracked electronically and database is updated regularly, to provide details such as material certificates, specifications, receipt date, purchase order details, storage locations / shelf number, etc. This update will be carried out on weekly basis. The material verification shall be done with respect to design specifications itemized on a checklist for the respective materials.
INSPECTION AND TESTING
In order to ensure that the entire works are constructed to the required standards and specification LOCATION X RENT A CAR shall conform to specified inspections and tests, which are to be carried out at every stage of the Driving activities. All measuring devices, instruments and other testing equipment shall be kept in good working order and maintained to required accuracy.
Measuring and test equipment shall be issued and returned under controlled conditions. Inactive ones shall be labeled with “Calibrated before use” While active items shall be reissued on a new requisition.
If equipment that is out of calibration has been used to test or inspect an item, as much as possible the item shall be re-inspected or retested as soon as the out-of-calibration condition is identified. All items inspected since the equipment was last calibrated shall be treated as suspect.
A separate record card carrying an identification of calibration status shall be kept of each gauge or instrument.
For routine task and hold points during Driving / installation activities on the work site, LOCATION X RENT A CAR shall inform the Client at least 24 hours in advance via electronic log book. In the absence of Client Rep.
LOCATION X RENT A CAR shall inspect materials in accordance with the material control procedures in order to verify that the specified requirements for the project are met. Acceptance shall be in compliance with quality documentations and approval by the Client before bulk purchase. The inspection shall entail date of manufacture and calibration among other parameters.
LEVEL OF INSPECTION
The following inspection levels shall be identified in each ITP:
- Performance Point (P): Inspection Point identifying the party responsible to perform the activity described.
- Hold Point (H): Inspection Point beyond which the work must not proceed without concerned parties signing off the inspection activity, unless a waiver has been received by LOCATION X RENT A CAR Prior notification to Client is mandatory.
- Witness Point (W): Inspection Point at which the presence of the concerned party is NOT mandatory. However notification for inspection shall be issued if witness point is not attend, otherwise LXR must proceed with the work after internal inspection and necessary records.
- Review (R): Inspection Point meaning that concerned party must check the issued documents and inspection / tests records and certificates for the execution of the work.
- Random Inspection (I): Inspection Point means that the presence of the concerned party is not mandatory. No certification is required but inspection/test may be carry out at any stage of activity. LOCATION X RENT A CAR must proceed with work after internal inspection provided shows that control and tests reports are available for review.
LOCATION X RENT A CAR shall ensure that the Inspection and Tests Status of Driving elements through manufacturing, dispatch and through installations, test and operation is readily identifiable. Equipment shall be inspected at the source or upon receipt for identity, quality, general dimensions, and for signs of damage prior to being released for use. Non-conforming elements identified during inspection or verification shall be tested in accordance with the control of Non-Conformance Procedure.
When required by the contract, shall have the right to verify at the source or upon delivery / receipt that purchased products conform to requirements.
CONTROL OF MONITORING AND MEASURING DEVICES
Inspection equipment are very sensitive instruments which results are used for acceptance purposes. They are required to have current calibration status, and are subject to inspection by the QA/QC Coordinator or his delegates to ensure their suitability for the intended purpose and to verify maintenance of records. Inspection measuring and test equipment are maintained and stored as per the manufacturer’s recommendation.
The selection of monitoring and measuring devices shall be based on the type of measurements to be made and the degree of accuracy required.
Only qualified personnel knowledgeable in the proper care and use of monitoring and measuring devices shall take measurements. When devices are not in use, they shall be stored and protected in such a manner as to prevent damage or deterioration.
CONTROL OF NON-CONFORMANCE
The main philosophy of control of non-conformance’s is to ensure that:
- Non-conforming products processes are identified and marked in order to avoid inadvertent use or installation or repetition of the process.
- Proper reports, including dispositions established and approved by authorized personnel for the resolution of non-conformance are issue and reviewed.
- Actions are initiated and followed-up in order to prevent future re-occurrence.
PREVENTIVE AND CORRECTIVE ACTION
The responsibility for monitoring corrective and preventive actions and the maintenance of corresponding records is the QA/QC personnel. The cause of non-conformities related to product, process or quality system shall be evaluated by the Project Manager/Engineer to ensure the prevention of occurrence of such non-conformance. Such actions may involve a hold in production and monitoring of the initial non-conformities to verify the effectiveness of the proposed resolution.
Preventive action shall investigate the possible cause of non-conforming product and the action required to prevent occurrence. The significance of any problem effecting Quality is evaluated in terms of its potential impact on such aspects of processing costs, safety and customer satisfaction.
Any resultant corrective or preventive actions taken to minimize the cause of the actual or potential non-conformities shall be commensurate with the magnitude or problems and risks encountered.
Records are maintained of all corrective actions and where applicable, preventive actions taken.
INTERNAL QUALITY AUDIT
The Project Manager is responsible for the development and coordination of programme of internal / external auditing to verify the effectiveness of the overall Project Quality Management System conceived for the project.
Audits are conducted by suitably trained personnel who are independent of the activity assessment and the findings approved by the QA/QC for review and Evaluation prior to internal distribution to all relevant parties.
Audits are conducted with the aid of the Project Audit Schedule and are carried out to an established procedure and written records produced in a standard format. Additionally, Audits are performed as required by the contract to identify aid action any particular activities or concerns as they occur. However, minimum of one audit per year per project shall be carried out.
Audit Reports identify:
- Personnel audited and Project
- Activities audited
- Corresponding to ISO 9000 elements
- Procedures or work instructions referenced
- Areas of conformance and specific non-conformance found.
- Where the results of internal auditing reveal areas of non-compliance with documented procedures, these areas are investigated to establish if:
- Reported deviations are not in compliance with the intent of the stated policies and objectives of the Project Quality Management System.
- Procedural changes are required to reflect actual current practice as part of the on-going development and improvement of methods of operation.
Audit findings are classified and reported according to their critically as observations or Corrective Action Requests. When Corrective Action Requests are issued with the audit report, the person responsible for implementing the Corrective Action is also to be identified. It is the internal Auditor’s Responsibility to propose appropriate action and future actions to prevent the deficiency from reoccurring.
Corrective Action Requests are forwarded to the Project Manager for the appropriate close-out. Corrective Action Requests are followed up by the third party (CONSULTANTS) and QA/QC Rep for effective implementation and close-out.
Reports of third party audits (CONSULTANTS) and external audits are directed to the QA/QC who ensures that the external / third party audit report are distributed to:
- Management Team
- Department Managers (as applicable)
- Auditee(s).
Audit findings reported in external / third party audit reports are dealt with the same manner as audit findings reported in internal audit reports.
DOCUMENTATION CONTROL
The receipt, issue, indexing, filing and storing of all documents relating to the contract shall be controlled at all times. A transmittal system shall be for the internal and external movement of all documents.
Control shall ensure those records of receipt; description, revision and distribution are maintained at all times. The distribution shall be determined and defined to ensure the correct edition of each document is issued to the workplace prior to the performance of the actively concerned.
All changes and revisions to documents shall be processed in the same manner as the original. Revision shall be clearly identified. All documents, which are subsequently cancelled or superseded, shall be clearly marked as such or removed from the site.
Information and data that is stored or transmitted by electronic means shall be subject to controls as stated above.
Corporate Documents
These are the designed documents that check, regulate and approve the quality standard and history of the work at hand. Examples of such documents are:-
- Quality Control Procedure (QCP)
- Method Statement (MS)
- Inspection Test Plan (ITP)
- Non Conformance Report (NCR) Procedure
QUALITY RECORDS MANAGEMENT
All documentary evidence which demonstrates achievement of the required project quality standards and scheduled milestones are to be systematically complied, distributed and stored for future references as required. They are to be compiled on a progressive basis, uniquely identified and filed so that data therein can be easily retrieved for analysis and to demonstrate achievement of the required specification requirements / targets. Quality records shall be maintained current with the actual place and progress of the work.
The project Manager is responsible for retention and maintenance of all documentation as follows:
- Certified material test reports and certificate of compliance.
- Heat treatment report charts.
- Non-destructive Test reports including radiographs for welded elements.
- Daily, weekly and monthly progress report.
- Change / deviation from original scope or material specification through CTQ.
- Inspection and test reports.
- Specific Quality Control tests for major project products. e.g.
-Concrete cube compression test, earth compaction test etc
- Quality Control Records
- Report of Non-conformities.
- Audit reports.
Project Quality records are compiled throughout the execution of the work for the close-out stage of the project. Records are assigned a retention category and are normally held for a maximum period of five (5) years, unless otherwise required by the contract.
MANAGEMENT REVIEW
The Management of LOCATION X RENT A CAR is committed to the review of its quality Plan bi-annually to meet up with relevant quality practices and to the customers’ satisfaction. We are committed to the continual improvement of our quality plan to the satisfaction of our clients and customers.
PROJECT MEETINGS
Project kick-off meeting shall be held after Award of contracts. Project Review Meetings are scheduled to be held fortnightly thereafter. It is the responsibility of Client to choose the meeting venue and nominate participants. The minutes of the meeting shall be taken by any nominated parties.
The Project Manager can initiate any meeting for LOCATION X RENT A CAR depending on the need e.g. on the spot assessment of driving issues in the site to proffer solution to the challenges.